Meet the Welder - Paul Smith from GET
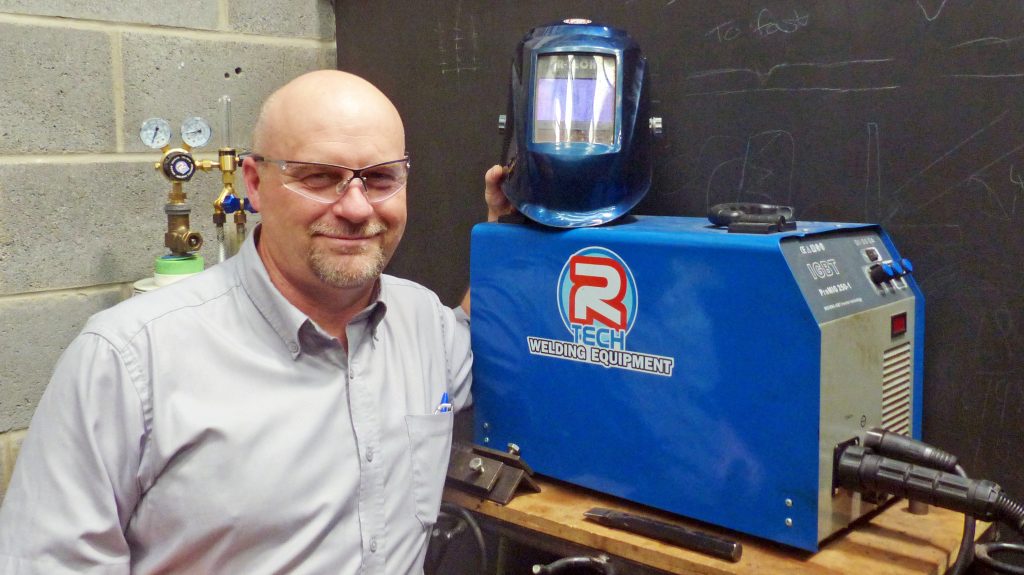
For over 40 years, Gloucestershire Engineering Training (GET) has delighted clients with tailored engineering training led by industry’s needs, raising industry standards, giving students a solid foundation in engineering skills, and ingraining the best-practice behaviours demanded by engineering and manufacturing. Meet the welder - Paul Smith, a welding professional with decades of experience, and currently one of the organisation’s lead instructors, has worked full-time with GET since 2014. During a recent visit, we dragged him away from the current cohort of 105 apprentices and met the welding trainer with a passion for joining metal, teaching, sipping Jameson and working on old Land Rovers…
R-Tech: How did you get into welding and progress your career?
Paul: My father was a traditional blacksmith-farrier, so I grew up around metalworking. The first thing I welded was the chassis of our old Morris Minor when I was 14; I’ve been welding ever since. When I left school, I got into the recycling industry, then transport and later construction equipment. Later still, fired by a passion for helping people develop their skills, and inspired by my instructor Maurice Westwood, I got into teaching, initially with Gloucester College and more recently with GET where I’m now a lead instructor on the Practical Team – specialising in welding of course.
R-Tech: What’s most rewarding about your work?
Paul: Passing on skills to our apprentices. In particular, it’s about seeing ‘the penny drop’ for a student, which can happen after a week or 11 months depending on the individual. It’s wonderful to see them realise that they ‘get’ welding and then watching their knowledge, skills and creativity blossom.
R-Tech: Do you prefer MIG, TIG or MMA welding?
Paul: All three processes have their place, depending on the job, but there’s something about the purity of MMA stick welding, and getting back to basics with metal, welding rods and a few amps, that really appeals to me.
R-Tech: What welding project (from any time in history) would you most like to have worked on?
Paul: Actually, it’s a welding project that I was involved with a few years ago when I spent a year working on the restoration of the pre-WW2 London fireboat Massey Shaw at Neilsens in Gloucester. The ship operated on the Thames in London during the blitz and was also one of the Dunkirk ‘Little Ships’ that rescued so many British troops from France in 1940. It was a demanding project but an honour to help preserve such an important piece of Britain’s maritime heritage.
R-Tech: Which R-Tech equipment do you use? What do you like about it?
Paul: We’ve currently got five bays set up, each with a TIG 201 and a MIG 250 machine so we can teach MIG, TIG and MMA. Being analogue machines, they’re ideal for teaching because it’s so easy to concentrate on the welding, rather than the machine – they’re perfect for demonstrating immediately what happens when you change settings during welding. The machines and the customer support from R-Tech are both first-class. Rob and his team have got us out of a few fixes over the years. I wouldn’t go anywhere else.
R-Tech: How do you see the future of welding?
Paul: It’s full of opportunities for the right people, not least because we face a massive shortage in skilled welders over the years ahead. That’s where organisations like GET come in. Of course, there will be more automation of welding in some parts of engineering, but lots of companies won’t be able to afford this. Skilled welders bring the versatility that robots can’t offer. The technology may advance, but there will always be work for skilled welders. Of course, if they happen to be working with robotic welding, understanding the principles of welding, machine set up and different parameters will still be essential.
R-Tech: What’s your top tip for novice welders – and seasoned pros?
Paul: For the newcomers, I say look, listen, see what the work piece is telling you and respond to it. For the old hands? Be open to new ideas, technology and processes, and willing to change.
R-Tech: Thinking back over your 35-year welding career, what’s the biggest lesson you learned and the most valuable piece of advice you received?
Paul: Don’t touch what you’ve just welded; it’s hot! As for advice, it’s something I picked up from Maurice Westwood, who was a wonderful trainer: learn to understand and work with the material rather than trying to fight it. Understanding how the metal will behave is one of the secrets of consistent welds and good penetration.
R-Tech: How do you unwind after a busy day?
Paul: Quality time with my family and two dogs – a border terrier and a Cockapoo – a glass of Jameson or working on two old Land Rovers.
R-Tech: You’ve been very generous with your time and insights. Is there anything you’d like to share before we let you get back to your students?
Paul: As a welder, I’ve never been out of work and have proved that you can shape a rewarding career around first welding and then teaching welding. The future is bright for young people who enter the welding trade with the right attitude, willingness to listen and learn, and determination to succeed. We’d love to see more women in welding and engineering as a whole, because, with only around 10% of our students being female, they’re still hugely under-represented.
R-Tech: And finally, you started welding on that Moggie Minor chassis all those years ago. What’s your next welding job?
Paul: Probably some Nickel-rod TIG welding or TIG brazing on a damaged milling machine cast iron knuckle we’ve got in the office, or some pre-MOT welding on my Land Rover Discovery 2. More chassis repairs – some things just don’t change with the years!
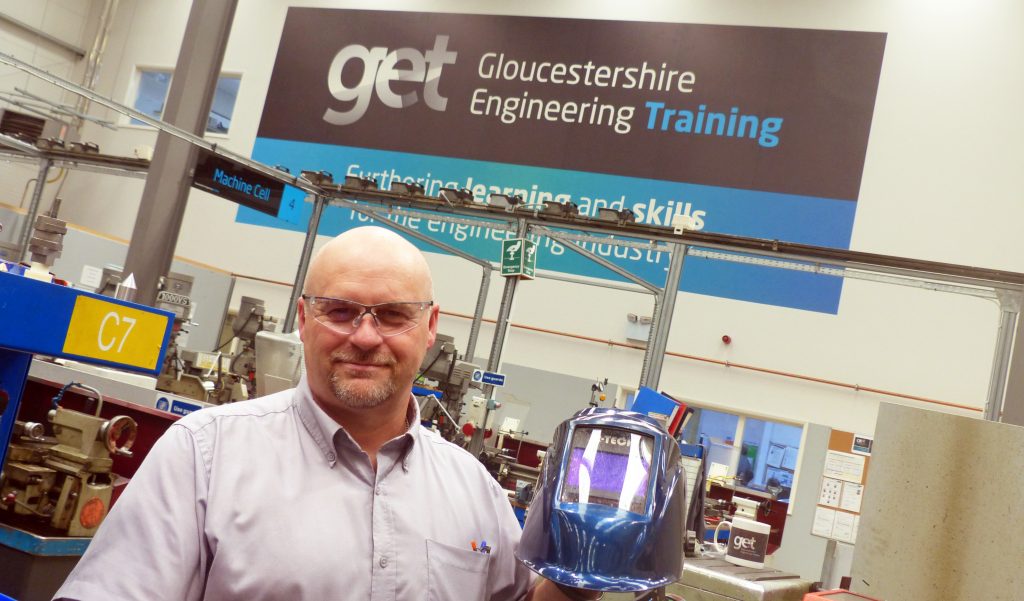
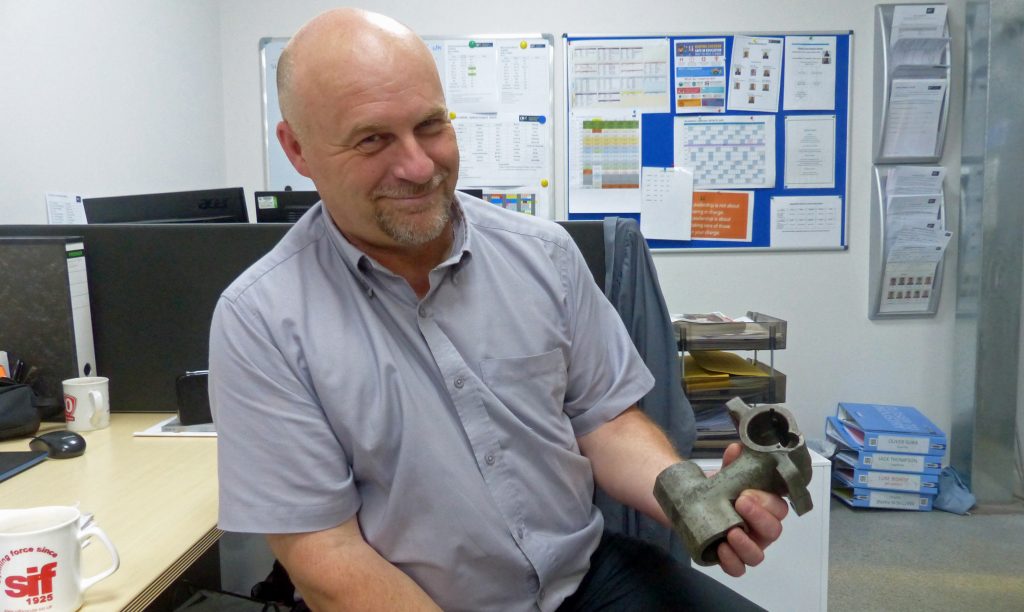
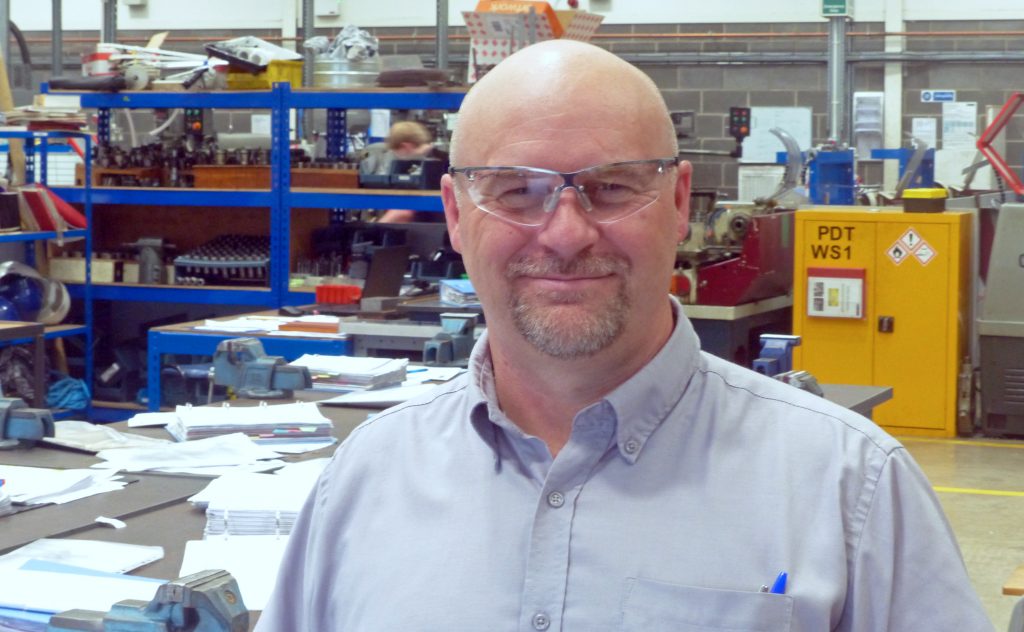
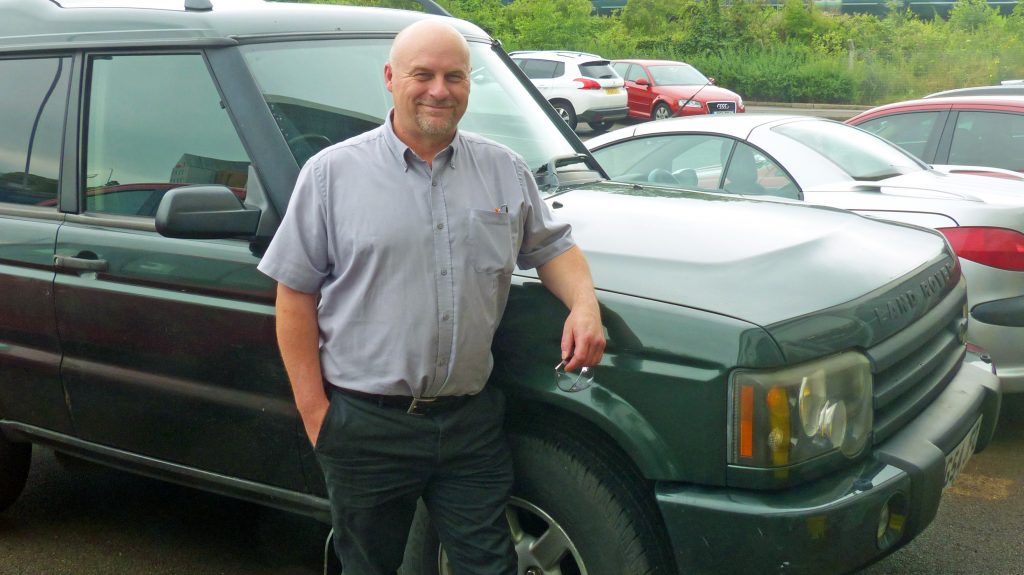