What is MIG Welding | How Does it Work?
Metal inert gas, better known as MIG Welding, is one of several welding techniques that use electricity to melt and fuse pieces of metal. But what exactly is MIG Welding?, since its invention in the early twentieth century, the appeal of MIG welding has grown phenomenally based on its speed and ease of use. The machines are relatively straight forward and we have done our best to keep this simplicity throughout our range of MIG welding machines.
MIG welding is a sub-type of gas metal arc welding (GMAW), a process that’s been widely used since the 40's. Since then, despite equipment details changing quite a bit, and reference to the process by various names (including gas metal arc welding, spray arc welding, flux-cored arc welding and short-circuit welding) the general principles remain the same.
You can read more in The R-Tech Welding Equipment Guide to MIG Welding
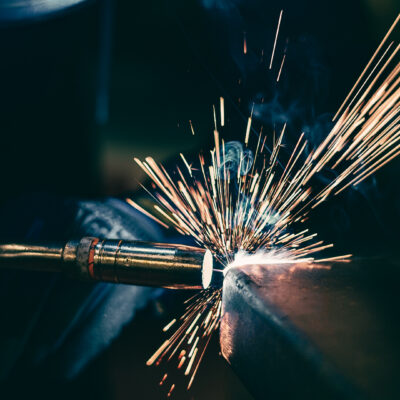
How MIG Welding Works
Whether you weld in your garden shed, a Formula 1 team’s workshop, or using production-line robots in a massive factory, MIG welding works on the following principle. Using lots of electricity, an electrical arc (a short circuit) is created between an electrode wire (a positive anode) and the parent metal that’s being welded (a negative cathode). The arc melts the electrode wire, which is then deposited to create the weld. When the heat is removed, the weld pool cools, solidifies and form a new piece of fused metal – the weld is made.
When you use a modern MIG welding machine like ours, spool-fed electrode wire is fed through a tensioning mechanism and into a co-axial supply line. This leads to a hand-held MIG welding gun – the MIG welding torch or ‘gun’.
At the same time, a shielding gas (typically argon, carbon dioxide or a mixture) is fed along the same supply line to the gun. The gas protects the weld pool from atmospheric gases that would otherwise weaken the weld.
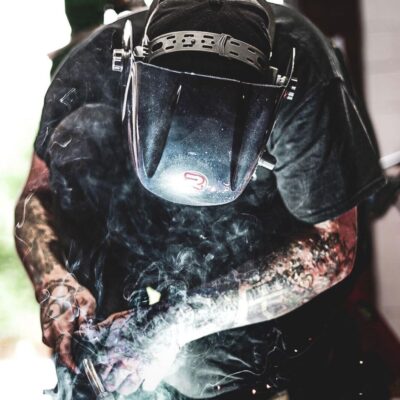
Avoiding Common MIG Welding Defects
R-Tech’s staff say: ‘From experience, most problems you will encounter with MIG will come down to one of four things. They are incomplete penetration, excessive penetration, incomplete fusion and whiskers. In each case the solution is pretty simple. To solve incomplete penetration, increase wire feed and reduce the amount the wire protrudes from the MIG gun. To correct excessive penetration, reduce the size of the gap you’re trying to fill. You can usually fix incomplete fusion by not allowing your electrode wire to get in front of the weld pool. As for those whiskers? Keep your wire at the front of the weld, make the weld pool smaller, and adjust the wire so it sticks out of the MIG gun less. Of course, for more helpful advice on MIG welding, our team is always here for you.’
MIG Welding Is Versatile
MIG is particularly versatile because you can use it to weld many different metals. These include carbon steel, stainless steel, aluminium, magnesium, copper, nickel, silicon bronze and other alloys.
Okay, so the MIG process isn’t the best choice for all welding jobs. But for a wide range of professional and amateur welding, MIG is the best solution. Let’s have a chat about your MIG welding challenge
As with any industrial process, MIG comes with advantages and disadvantages. The good news – as millions of amateur and professional welders already know – is that for a vast range of welding tasks, the advantages outweigh the disadvantages. Here are some of the main ones:
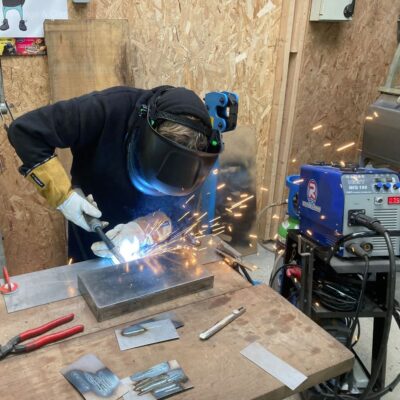
Advantages Of MIG Welding
MIG is fast. That’s mainly due to the continuously-fed electrode wire and the way it reduces the amount of stopping and starting during welding jobs.
It’s suitable for joining many different metals and metal thicknesses too. A characteristically good weld bead and the ability to vary weld penetration by changing the amount of current makes achieving strong, smooth welds remarkably easy.
All-position welding capability: MIG handles horizontal, vertical or flat welding with confidence.
There’s minimal clean-up requirement. Only TIG welding is cleaner; compared to traditional stick welding, MIG doesn’t use flux, or create extensive, messy weld spatter and slag.
High-deposition MIG enables ‘long weld passes’ so you can deposit more metal with each pass and use fewer passes to weld a large joint. The result? Faster welding and increased productivity.
Avoidance of waste: unlike stick welding, which typically wastes part of each electrode (electrode stub loss), continuously-fed wire means you use all your electrode during MIG welding.
MIG is easy to learn, mainly thanks to the fact that several parts of the process are automated.
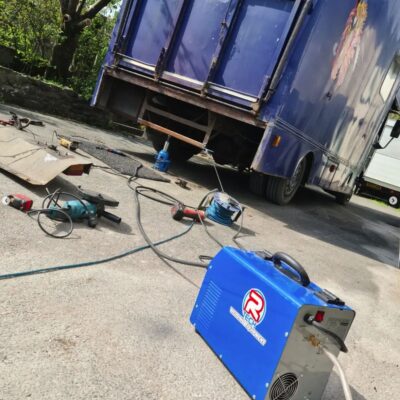
Disadvantages Of MIG Welding
MIG needs a bit more initial investment in equipment compared to traditional stick welding. However, the specification, capability and reliability of today’s best MIG machines is impressive. For serious professional or hobby welders, modern machines offer great value for money.
Higher maintenance of MIG equipment? With modern, reliable machines (and our free loan machines), this argument needn’t apply.
MIG can only be used on thin to medium-thick metals (typically between 0.6mm and 14mm).
There’s an argument that MIG is less portable than other welding processes that don’t require an external gas source. This may be true sometimes, but compact modern MIG welders often redress the balance. For lots of professional and amateur welding, MIG is the preferred method.
Compared to tungsten inert gas (TIG), MIG welding may give less controlled welds under some circumstances.
Outdoor MIG welding can be more difficult because of the effect of wind on the shielding gas. Then again, this can often be solved with higher gas pressure, portable wind breaks or even gasless wire…
So there you have them, the main pros and cons of MIG. As you can see, modern MIG equipment and thoughtful customer service details (such as free loan machines) make some of the traditional ‘disadvantages’ much less of an issue…
MIG Welding Equipment
We built our service for welding professionals and amateurs on supplying reliable, high-quality equipment. All our machines are easy to use and proven in the most demanding welding environments and offer exceptional value – just read customers’ reviews. Then there’s the reassurance of our direct customer support. It begins with your first enquiry or information request and continues as you choose, use and add to your welding equipment.
Forget the inconvenience and delays of going through distributors who don’t make and service welding equipment themselves. With R-Tech you deal directly with the manufacturer.
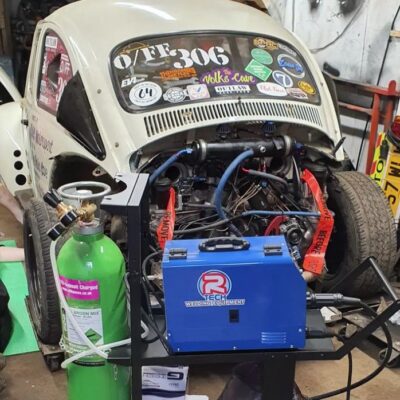
Built To Last
All our machines are robustly built in metal casements. And they all use the latest ultra-reliable inverter power components from American and German companies. These include class-leading Siemens IGBTs rather than inferior MOSFET electronics.
To keep whole-life ownership costs as low as possible for welders, we design and build our MIG welders on a modular basis. That means they can be maintained and repaired at component level. We also supply them with industry standard Euro Style torches so you won’t have to replace the whole welding machine in the (unlikely) event of an issue with a torch.
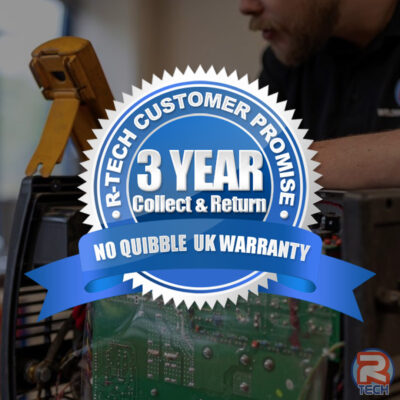
Trusted Support And Support
Finally, we back every R-Tech welding machine with a no-quibble three-year ‘collect and return’ warranty and a reassuring 10-year duty of care. It all adds up to minimising long-term running costs of your R-Tech machine – while you get on with welding.
By the way, if your portable MIG welder ever needs to visit our – not very busy – repair department, we’ll lend you another machine free-of-charge so you can keep making money or enjoying your hobby.
Email us now salesdept@r-techwelding.co.uk or call 01452 733933 for help and advice.