Meet the Welder - Trevor Hatton
Panel Beater for Race & Restoration, YouTube Blogger & Classic Car Fanatic
Last week I popped round to meet the welder, Trevor Hatton at his home to have a chat and a cup of tea. With 30 years experience in the accident and repair trade he really knows his craft! He also has a project on the side restoring and converting a 1960's Bedford van into a mobile coffee and cake van which he has created a YouTube blog for the progress and also for showing 'How to' videos .
R-Tech: How did you get into the industry?
Trev: I started in 1986 in a YTS scheme with Haines & Strange as a trainee panel beater but this only lasted a year as they decided that they were not going to keep the YTS scheme going so I was out of a job!
My Uncle offered me a job in his garage called Winchcombe Motors, he had a panel beater that had left and that the guy who was left behind could help train me up. So I went there and it was stuck in the dark ages! They were still gas welding, oxyacetylene welding and only a little MIG welding. I stayed there up until 1992. That was when I decided to make a break for it and get my own place.
I ran my own restoration company restoring old Morris Minors from 1992-1999, with regards to the welding I just MIG welded during this time. In 1999 I had recently got married and wanted to start a family. The problem with restoring value less cars or cars with little value in, although they are nice and people are passionate about them, people evaluate the value of your work to the value of the car. Some people can see past it, the value of cars can rise but some people don’t want to spend more than their car is worth. Work was not consistently coming in so for a bit of security I decided to go back into the accident and repair trade. I worked in many different places! I worked at Lex Body Centres, Venture Exclusive which then became Gemini and then I did a stint at Blade Westgate, and then I went to Gloucester Gemini, and then I went to Bayliss Haines and Strange in Cheltenham and I stayed then up until 2014..ish.
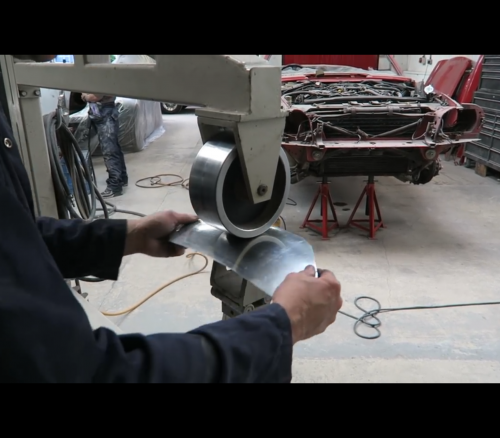
R-Tech: How did you find working in the industry?
Trev: The accident and repair business was undergoing huge changes because they had introduced this new British Kite Mark ATA pass 125. The good thing about this was that we were doing things on cars that we shouldn’t have been doing but we didn’t know! We were welding high strength steels on cars with MIG welders and we didn’t know any different.
The methods that were introduced to the industry, some of them were as thick as a telephone directory! Of course, we were not given any extra time to read through these but you then still have to sign your name to the repair and can be held accountable in court if there was an accident! Work was very pressured and everything was monitored in terms of time. It felt like there was never enough time to do a proper job and the only way that you could catch up would be to cut corners. This was why ultimately that I thought enough was enough! At the end of the day you work because you enjoy doing your job and you get paid for your skill but if you're not getting either out of it you’re not going to stay!
R-Tech: Where are you working currently?
I am currently working at Race & Restoration in Winstone, just outside of Cirencester. I have been working for Steve for about 5 years now. It is a great place to work as I get to work on cars that I wouldn't even dream of even being able to get close to! I get a huge amount of job satisfaction helping to keep these cars on the road.
We have a few projects on the go but we have recently been working on a historic race car called an Allard. It is being re-created by the Grandson of the original designer.
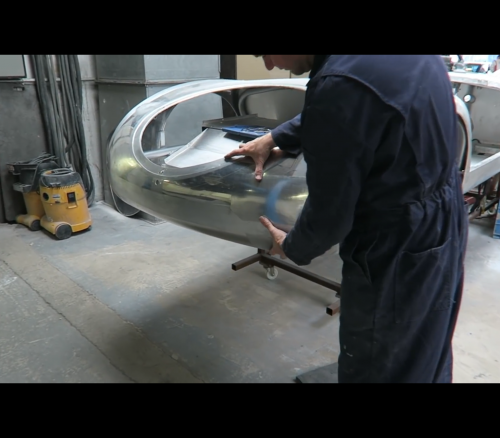

R-Tech: So having MIG welded for most of your career how did you get into TIG welding?
Trev: I thought to myself ‘How hard can this be?’ I have always learnt on the job. Having worked mostly in the accident and repair industry things are done differently but there are a lot of similarities. I wanted to be productive and I always want to learn new things so I had to keep a balance of learning on the job and getting on with my job! So I picked up the TIG welder and started using it and it immediately took me back to my oxyacetylene days.
I had a couple of teething problems to start with, I kept touching the end of the flaming rod on the end of the tungsten and then I learnt that you don’t do that!! What I do now is have 7 or 8 tungsten’s sharpened and ready to go! Initially I found that I was hitting it too fast with the rod and found that there was too much build going on, so I relaxed off that and got over the fear of it blowing a huge hole in the material. I have learnt to let it do what it wants now!
I persevered with it because it was much better to use on the outside of cars. I stuck to steel initially but then we had a job come in that needed aluminium welding on a newer Ferrari’s and Steve was going to call in this chap to do it. I said to Steve ‘I’ll have a crack at it and if it starts looking like it is going to turn into a mess then I will just stop’. I picked up the TIG and found that it was virtually the same as welding the steel really with just a few changes and the characteristics.
We were getting by with a MIG welder but we needed a TIG welder for the aluminium work. Steve bought the TIG161 and used to bring a chap in to do the bits of TIG welding that we needed doing. During an exceptionally busy period we had an aluminium job come in, the guy that normally did the aluminium welding, (Morgan trained) had to be booked which meant a wait of a couple of days so I just got on and did it and it all turned out spot on, I’d practised welding aluminium many times but not on an actual car so this was the time I needed to put into use what I’d been practising.
Using a TIG welder has opened up a world of possibilities for us.
R-Tech: Do you prefer MIG or TIG welding now?
Welding is a very small part of my job really; my job is to fabricate panels. For instance, we get a customer come in with their classic Ferrari and a section of the front wing has rusted. We cut out the rust and I have to make that replacement section out of a flat piece of metal. The problem for me with MIG welding the section on was the distortion issues. You end up destroying all your hard work using a welder that you don’t have much control over.
This is where the TIG welder helped because I wasn’t getting the heat distortion and the weld was self sealing. So I have now got it to a point where I can get the panels fitting so well that they will almost weld themselves together with virtually no filler rod. If I am welding on steel then I will use a little bit of MIG wire. If I use a filler rod it kills the pool so then you have to turn the power up and you end up with a situation where there is too much heat. So when I am welding steel, every 3mm or so I will offer up a bit of the MIG wire somewhere near the weld pool and a little bit will bead off and zip into the pool and add a little bit of residual. You have a slight amount more there than you need and this way when you are finished and you grind the weld off you have no undercut, it is just like a perfectly flat weld. This has helped me enormously in my job. Just being able to MIG weld before was tricky for me because I would have fabricated this beautiful panel and then I would think ‘How am I not going to obliterate it with the MIG?’!
R-Tech: How did you start up your blog, how did it come about?
Trev: Well I had invented this machine which I called an ‘Auto-Shaper’, I couldn’t think of anything else to call it! When you apply filler to a car you then spend hours and hours rubbing the filler out and I looked at this and I thought if you could automate a part of this process it would save a huge amount of labour. Body work is a funny thing, sometimes you spend a lot of time preparing the panel you might spend 2-3 hours rubbing down the filler, and then you go to paint it and if it isn’t quite right then you have to fill it again and start the process all over again. So I made the machine to take out a lot of the work in rubbing down the filler. I couldn’t think of a way to promote this machine and then I thought the easiest way has got to be the internet. I used to watch YouTube all the time so I created a channel and a video of the machine. Then I rang around all the insurance companies, the tool manufactures and nobody believed it! They all basically said ‘It’s an April fool’s joke’ ‘It’s a hoax’ and that was the kind of response that I got and it got hardly any interest. The only way that I could have convinced them that it wasn’t a joke was by showing them exactly how it worked and that would have given away the invention design. I spent a few weeks promoting but it never really took off, even though I still get messages about it now. So I decided not to pursue it but left it up.
When I started work on the van I decided to put it up on YouTube because I thought if I get stuck someone will come forward and offer my some advice, and that is exactly what happened! It has turned into an epic project, it has gone on far longer than I ever would have dreamed because I have not been able to hold myself back from building more things into it, I haven’t been able to rein it in! I have gone mad with changing things on it but I really didn’t know what I was doing so I have learnt through doing it.
The followers grew on the channel with each episode that went on. Then people started to ask ‘Why don’t you show us how you did that?’ ‘Why don’t you do a tutorial on how you welded that together?’
So that is what I started to do because where body-work is concerned people had enormous trouble welding thin material without it warping and buckling out of shape. I have been working with MIG welding for so long that I have worked out all of these techniques but I am only talking mild steel it is safe on and this is a bit of a crossover problem that I have with people saying that ‘You shouldn’t be showing people how to weld on a car with inappropriate techniques’ but they are talking about new cars and I focus on old/classic cars. I have worked out various ways of making heat syncs so that the welding wouldn’t warp the material and to prove the theory I have smashed things up after welding it to show that the weld will hold together, like a strength test.
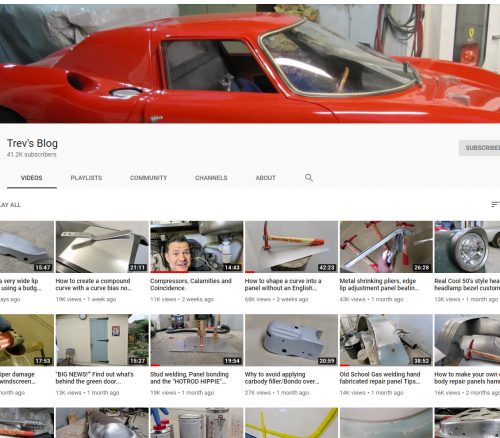
R-Tech: Tell me about the van, how did this project come about and how has the restoration gone?
Trev: She has been off the road since 1981. The original owner bought the van and ran it into the ground and then put it in his garage along with a Vauxhall Cresta.
He was a builder; I had all his old business cards still piled in the roof shelf! There were also loads of receipts from 1960 something or other for all his building materials! There was also the original tax disc dated 1960 so I am going to get it copied and stick it in the window!
I had to replace the bodywork from about ¾ of the way down. She was totally rotten. So I cut it all out and fabricated all new panels. I have engineered the lift up door on the side of the van for the catering and also had to change the way the passenger door operates because it was a sliding door. She has got new wings and wheel arches.
It is literally made out of about 100 different cars now! The door hinges for the passenger door are off a rear door of a transit van and the pull catch for the side door is off a Honda Civic! It was a case of whatever I could cannibalise from the scrap yard. I had to because you cannot buy anything for this van. Nothing is available any more.
I replaced the engine with a Ford Focus 1.8L petrol engine which will be far more economical and reliable. The old engine would do 45mph and 19 to the gallon and needs a complete rebuilt every 60,000 miles!
I had to redesign everything; the dash would have been open to the engine originally and I have boxed it in now to make it weather proof. It went in reasonably straight forward even though it was half as wide again as the original and it hit the steering so I had to redesign the steering which took me about 3 months of head scratching. I have had to create a whole wiring system for it so it will run off the Focus engine; I had to re-gig the fuse box so it would do what I needed it to and it all works!
I am currently getting the lights in, door handles and all the fittings done. The original seats were completely trashed so I found some ex ministry of defence old stock, Bedford truck seats, being sold on EBay. They weren’t the exact same ones but I could make them fit. However they were black and didn’t look right in the van. So I took the covers off and sent them off to a chap who copied the pattern and he made these lovely blue and cream ones.
Originally she was green. I have used a decent brand of paint for the exterior, Dupont, it goes on quite flat and polish’s up nice and it will last, UV resistant, I wanted the longevity so paid the extra and used quality. There is about 20L of primer on there! I proxy primed the steel to make it nonporous, like they use on boats, hopefully nothing will attack the metal now. I have painted some wheels for it red and there will be some red in the sign writing to break up the blue.
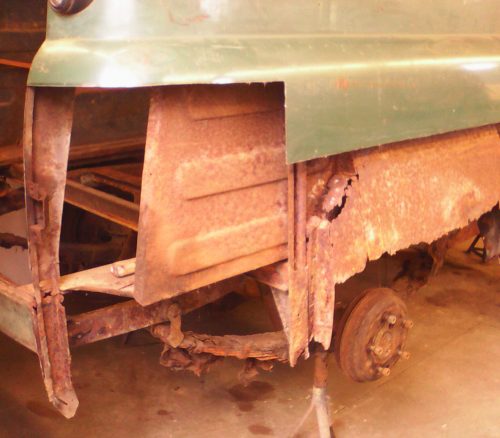
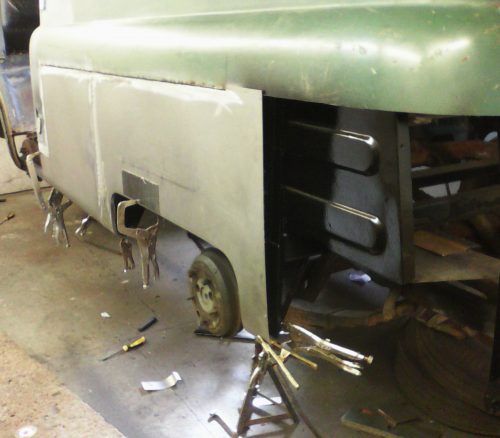
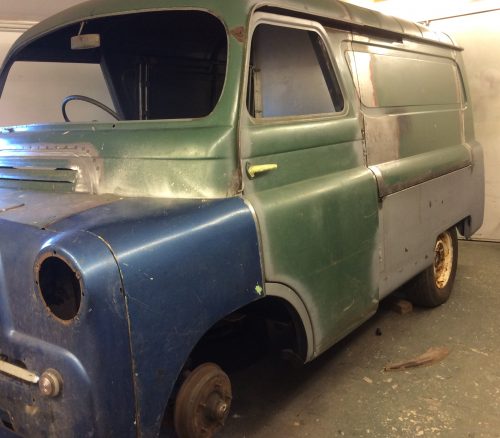
R-Tech: When the van is finished what is it going to be used for?
Trev: The idea is to go around and sell coffee and cake at vintage motor shows. My wife is mad about baking! We have got an old vintage style awning that will pull out over the side opening to keep the sun and rain off. It is red and cream striped with a scalloped edge and I have made a framework that attaches it to the van. It has a gas powered coffee machine and I have put the gas bottle inside the van that is an LPG tank and I can fill it at a petrol station. I have boxed it all off and it is vented through the floor, I didn’t want it outside the van as it looks untidy.
I wanted something unique and not something that was just hashed together so I have taken my time and got it to what I wanted. I wanted it to be a story really. We are going to start up a second YouTube channel when the van goes on the road to follow the business and my wife will do baking tutorials. We have sourced a fantastic coffee supplier and our eggs for the baking will come from a company called Cackle Bean who have these chickens on a special diet so that the eggs are almost a fluorescent orange and they make a very yellow Victoria sandwiches! We are going to use Shipton Mill flour, we are going to meet them and we will do a blog about it.
We want the romance of the thing really, get to the shows on our own steam, serve customers and then drive home. We have now got our registered trade mark ‘The Baking Bird’, my wife’s nickname is Birdie. Now we have the name registered we can get the van sign-written and get the cups printed with the logo. It is now getting to the point where it is now weeks of work not months of work so I am really looking forward to getting it finished and out on the road.
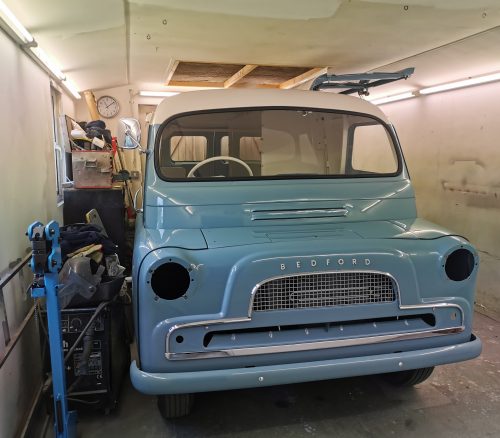
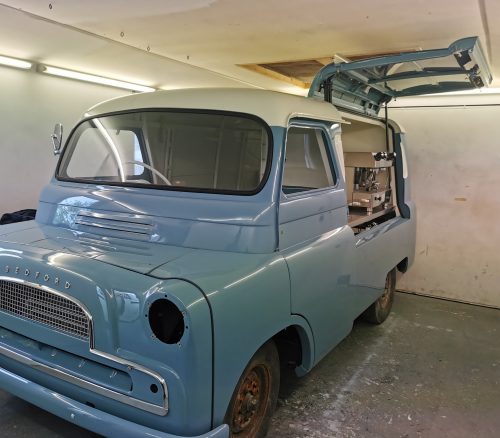
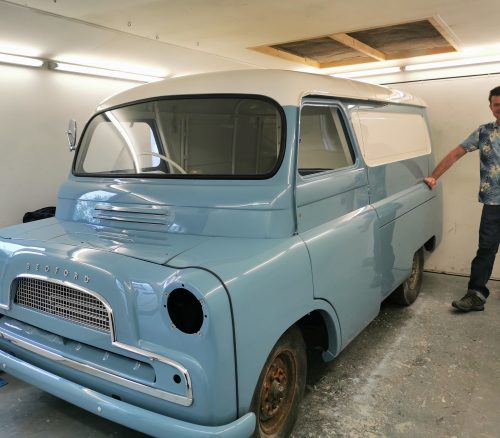
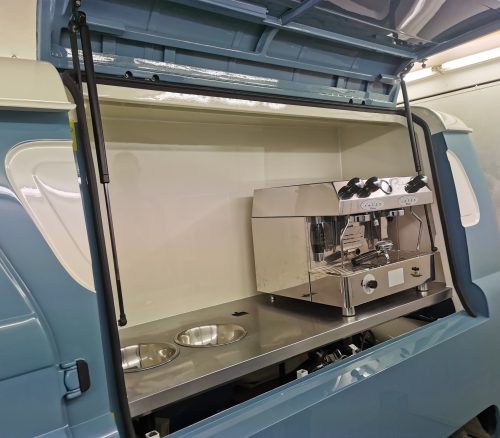
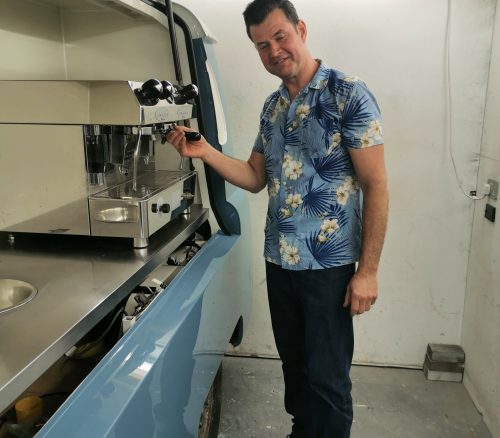
